このページでは、「SHOWAイラストレイテッド」として企画された
本社1Fギャラリーの展示をご紹介いたします。
昔の、今の、そしてあの時の、“昭和鉄工ストーリーズ”です。
- 01
ロイヤルトレインを暖める
明治天皇お召し列車の暖房器具
- 02
フクシマからのオファー
原発作業員待機所のための仮設クーラー
- 03
アルミホイル3枚分の発熱体
厚さ30ミクロンのステンレス箔ヒーター
- 04
29年後のスケッチ
天神地下街の鋳物大天井
- 05
サナギのような鋳型
蝋から金属に─ロストワックス精密鋳造
- 06
福岡、橋のある四景
記憶に残るプロダクト─ 鋳物の欄干
- 07
輸入品を駆逐した傑作機
男たちの悲願が結実した「アサヒボイラー」
- 08
総動員の1号機出荷
8年後のビッグタイトルへの結実
ロイヤルトレインを暖める01
明治天皇お召し列車の暖房器具
写真は明治時代のお召し列車の皇室用客車である。当時は純“メイド・イン・ジャパン”の工業製品はまだ少なく、列車の機関パーツも海外製に頼っていた。そんな中、1910(明治43)年に明治天皇の御乗用として鉄道院新橋工場で製造されたこの「6号御料車」は、日本近代製造業の技術を結集させた国産車両であった。
本車は、内装・外装とも歴代の御料車のなかで最も壮麗なものとして評価された。次の「7号御料車」が落成したあとも大正天皇がしばしば御乗用に選んでいたという。この客車を暖めたのが我々の鋳鉄製ラジエーターだ。創業者の斎藤一自らがデザインした細かな装飾はいかにも贅沢で、菊花紋章と相まって工芸品のような趣である。
宮内省がわざわざ福岡の企業を選んだのは、当時我々が唯一のラジエーター国産メーカーだったからだ。その頃すでに海軍省や大蔵省に暖房器具を納入しており、実績も認められていた。国産化を推進してきた当社の姿勢が国の政策と見事に合致したと言える。
このラジエーター納品以降、我々は鋳鉄製ボイラーの国産化にも成功し、後年“東洋一のボイラーメーカー”と呼ばれるまでに至った。もととなった熱技術と鋳造技術は、100年以上経った今日も当社を支える基盤として受け継がれている。
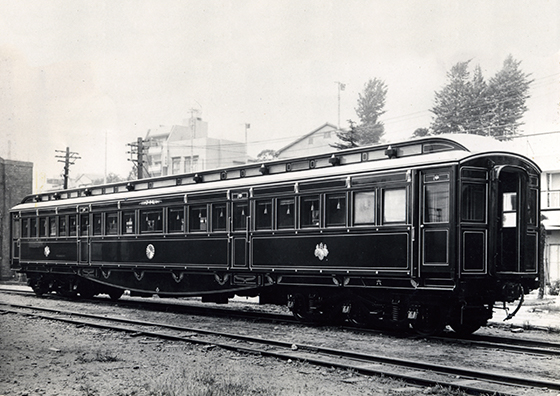
-
お召し列車用ラジエーター
H485×W270×D330 鋳鉄製
フクシマからのオファー02
原発作業員待機所のための仮設クーラー
いま大地が揺れたら命を落とすかもしれない――ただならぬ緊張感と大いなるストレスのなか、福島第一原子力発電所における未曽有の事態と闘う作業員や職員たち。東日本大震災の直後、彼らの束の間の安息地として選ばれたのは、事故を免れた福島第二原発の体育館だった。
夏がやってくる前に休憩所にエアコンをつけたい――依頼があったのは4月である。残された時間は少ない。ドレン水の発生しない仮設クーラーの製造にすぐさま着手した。
連日報道される現地の予断を許さない状況に全社員が奮い立つ。最優先の課題として取り組み、部署の垣根を超えて支え合った。スタッフと工場をフル稼働させた結果、6月には第1ロットの納品を果たすことができた。
この写真は設置直後に撮られた。左端に並ぶ円筒形のものが製品のクーラー※である。ダクトによって冷気が屋内をめぐる仕組みで、仮設ながらも高い性能を発揮した。窓からは日が差し込み、フロアには多くの木製2段ベッドが整然と並ぶ。手前には作業員のものと思われるタオルが干され、壁には子どもたちからの寄せ書きが何枚も見える。過酷なフクシマの現場を日本国中が支えていた。
※製品名は「シャワークーラー」、納入先は新日本空調株式会社。
仮設クーラーと数々の寄せ書き
体育館いっぱいに設置されたベッドと中空に吊るされたダクト
アルミホイル3枚分の発熱体03
厚さ30ミクロンのステンレス箔ヒーター
それまで我々が扱ってきた暖房や給湯のための熱源は、燃焼技術を使った製品が主であった。1990年代後半、ひとつの転機が訪れる。いろいろなきっかけが重なり薄型の電気ヒーターの製品化に取り組むことになったのだ。何百キロもある鉄のボイラーを作ってきた我々にとっては試行錯誤の連続であったが、幾多の苦労を重ねて遂に新しい熱源が生まれた。それがステンレス箔ヒーターである。
箔という名称のとおり、とにかく薄い。家庭用アルミホイル3枚分ほどしかない。金属箔に特殊な加工(エッチング)をほどこし、通電させて発熱体に変容させる仕組みだ。スペースが狭い場所でも熱源を確保でき、またフレキシブルに形を変えられる。機器に内蔵して加熱・予熱・乾燥に利用したり、工場の製造ライン装置に用いて材料の焼成や熱処理に利用したり、その用途は幅広い。基材を変えれば飛行機の機内食トレイの温めから液晶用ガラスの焼成まで対応できる。従来の熱線に比べ大きなアドバンテージとなるその薄さと性能は、これからの熱源の可能性を大きく拡げた。
将来、卓上のカセットコンロやホットプレートはテーブルクロスに一体化するかもしれない。冬場はヒーター付きの靴の中敷きが当たり前になるかもしれない。工業用から家庭用まで、30ミクロンの発熱体には未来のアイデアが詰まっている。
ステンレス箔ヒーターを樹脂でサンドしたポリイミドヒーター
サーモグラフィで見る箔ヒーターの均一な発熱
29年後のスケッチ04
天神地下街の鋳物大天井
福岡市の天神地下街は連日20万人ほどが行き交う。その天井には29年越しのストーリーがある。
1976(昭和51)年に開業した天神地下街で採用された他に類を見ない鋳物の大天井は、排煙性、耐荷重、精度といったさまざまな課題をクリアして実現した。その29年後、2005(平成17)年の延伸工事で生まれた新街区では、機能性や安全性に加え、高いデザイン性の追求というハードルが待っていた。
新街区の環境デザインは佐藤哲哉氏に任された。彼が地下街の並行する2本の街路のために用意したのは、冬の道を想起させる梢(こずえ)と夏の道の葉梢(はずえ)のデザインである。あまりにも絵画的かつ彫刻的なスケッチは、メーカーにとっても「大いなる挑戦」を意味した。造形的解釈、図面化、鋳型製作のための立体化、鋳造方法など、全てのプロセスでスタッフ間の葛藤と格闘が繰り返された。
写真は葉梢天井の製品検査時に撮影されたもの。スケッチがいくつもの段階を経て、初めて金属に生まれ変わった瞬間である。塗装前の鋳物素地がモノクロのデッサンのような柔らかい陰影を見せている。実は開業時のデザインを担当したのも、若かりし頃の佐藤氏である。29年の齢と経験を重ねたデザイナーは、鋳肌を確かめるようにそっと手を置いた。
新天神地下街葉梢の道
佐藤氏による葉梢のスケッチ
サナギのような鋳型05
蝋から金属に─ロストワックス精密鋳造
サナギは幼虫が成虫になるために必要なプロセスである。成虫に似た形の殻の中で幼虫は一度どろどろに溶け、徐々に成虫としての形を成していく。まさにサナギの殻は成虫という鋳造品を生む鋳型のようだ。
蝋(ワックス)の特性を活用した「ロストワックス鋳造」の工程は、数ある鋳造法のなかでも特に昆虫の変態を思わせる。まず完成品と同じ形を蝋で再現し、それを砂でコーティングしたものがサナギでいう殻だ。それを高温の蒸気にさらして蝋を溶かし出すと中は空洞になり鋳型となる。あとは焼成した鋳型に溶かした金属を流し込むと完成だ。
ロストワックス鋳造は、いにしえから日本では仏像に、西洋では美術彫刻の製作にも用いられてきた。形や肌の再現性が高く、割型には必要な「抜き勾配」も要らないため、現在は主に精密な工業用部品や指輪等の装飾品の製作に用いられている。もちろん昆虫のような複雑な形も再現可能だ。
写真は金属が固まった後、砂の一部を取り除いた鋳型である。殻の中の蝋が金属に変質したかのように生まれ変わっている。やはり鋳型は人の手によるサナギと言えまいか。
ロストワックス精密鋳造品
ワックスを砂でコーティングしたツリーと呼ばれる鋳型
福岡、橋のある四景06
記憶に残るプロダクト─ 鋳物の欄干
日本人だけでなく、世界中から多くの旅行客も集まる福岡の観光スポットには、4つの印象的な橋がある。
西日本最大の歓楽街・中洲のど真ん中に架かる「福博であい橋」は欧風のクラシカルなデザインが特徴だ。ウォーターフロント副都心・百道浜の「福岡PayPayドーム」を臨む「よかトピア橋」はレンガ壁と鋳物スクリーンが風景をほどよく演出している。博多湾につくられた人工アイランドシティと箱崎ふ頭をつなぐ「香椎かもめ大橋」は新しい街へと誘うモダンな橋面が目をひくだろう。太宰府天満宮にある「御神橋」の擬宝珠は緑の中で真紅の塗りが色鮮やかに映えている。それぞれに意匠を凝らした欄干は全て昭和鉄工製である。
1970年代後半、我々はボイラー製造によって培われた鋳造技術をもとに、鋳鉄製高欄を中心とした都市景観事業へと進出する。景観材を手がけることで初めて自社製品が道行く人の目に留まるようになった。それは写真や映像に、そして何よりも人の記憶に刻み込まれていく。企業風土にはデザインという新しいマインドが芽生えていった。
今日もたくさんの人々が橋を渡っている。観光客が橋の上でスナップ写真を撮り、若いカップルが川面を眺めながら愛を語り、学生たちが仲間とはしゃぎながら通り過ぎていく。その風景の一部にあることが、なんとも誇らしい。
当社の高欄は主にダクタイル鋳鉄にて製造される
90年後半から開発した街路柵ではグッドデザイン金賞等を受賞
輸入品を駆逐した傑作機07
男たちの悲願が結実した「アサヒボイラー」
ボイラーの国産化が創業者・斎藤一の悲願だった。1915(大正4)年、彼は初の国産鋳鉄ボイラーであるストレーベルボイラーを世に送り出したが、まだ輸入品を凌駕するまでには至らない。
1931(昭和6)年、2代目社長の飯田久次郎がアサヒボイラーを発表。当時、世界的に著名であったアメリカンラジエーター社の製品をモデルに、日本の石炭に適合させ、かつ国内法令に適応できるよう研究開発したものである。燃焼工学の最高権威であった東京工業大学の関口八重吉博士主導の公開実験でも優秀な結果を残し、世界レベルをも超える高いクオリティは「鋳鉄ボイラーの最高傑作」と称され、世に喧伝されていく。
斎藤一の甥で商社を経営していた斎藤省三も、未だ輸入品が幅をきかせる業界に忸怩たる思いを抱いていた。アサヒボイラーが発表されると彼は、当時、三井・三菱・大倉と並び四大商社の1つと称された浅野物産と当社の提携を実現させる。これにより国内はもちろん、需要が高まっていたアジア諸国にも広く売り出されることとなった。
性能と販路を保証されたアサヒボイラーは瞬く間に市場を席巻。20数年に渡り、国産鋳鉄ボイラーの決定版として業界に長く君臨した。そして何よりも、明治維新以降数十年続いた海外製暖房用ボイラーの輸入を完全にシャットアウトしたのである。
当時のカタログ
商号が斎藤製作所の頃の社屋と社員(大正終わり頃)
総動員の1号機出荷08
8年後のビッグタイトルへの結実
極寒の12月の夜、A工場には煌々と明かりが灯っていた。空調機組立ラインには技術部と製造部のスタッフが総動員している。新製品「ラデック」の初出荷は想像以上に手間取り、朝からの作業はまだ続いていた。現場搬入時刻はとうに過ぎている。冷え込みが強まる中、ある者は潜り込んで配線を引き回し、ある者は脚立の上でレンチを動かし続けた。途中皆で夜食のカップラーメンをすすり、ようやくトラックを送り出したのは夜半過ぎのことだった。
「ラデック」1号機が採用される広島市中心部の銀泉広島ビル前は車線を潰して交通規制が敷かれていた。大型クレーンと作業員がしびれを切らして待つ中、夜通し高速道路を走ったトラックが遂に現場に到着した。早速荷台の「ラデック」が吊り上げられ、慎重かつ迅速にビル屋上に搬入される。同時に地上では規制解除にむけた復旧が大急ぎで始まった。全ての作業が終了したのは、まさに街が動き出すギリギリのタイミングであった。
リタンエアデシカント除湿方式によって外気湿度を処理する「ラデック」は、空調システム全体の省エネ化が可能だ。机上や実験室でその性能は確かなものだったが、銀泉広島ビルという実際の現場で初めて検証されることになった。果たして、1年後客先から報告された数字は、リニューアル前よりも61%のエネルギー削減という絶大な効果を示すものだった。
1号機納入から8年経った2019年、その後実績と改良を重ねた「ラデック」は、省エネ大賞の最高賞である「経済産業大臣賞」の栄誉に輝いた。あの寒い夜の熱い思いが実を結んだ瞬間だった。
技術・製造スタッフが総動員したA工場でのラデック1号機の出荷風景
採用された「銀泉広島ビル」(左)と屋上に設置された実際の1号機(右)